A visit to Kevin Clijmans in Arendonk at one of the Pluriton hatcheries. This hatchery has a capacity of between 16 and 18 million female day-old chicks annually, and also regularly supplies day-old chicks to Dutch rearers. Every day, a team of 24 lay the foundations for strong and healthy laying hens. “As the hatchery manager, I keep a watchful eye on everything and oversee the entire process”, is how Kevin sums up his work.
Kevin Clijmans has been the hatchery manager here since 2019. In this role he is responsible for the quality and technical aspects at the hatchery. A role he fulfils with passion for his profession. “I arrive at 6 am and start up the processes,” Clijmans begins his story. “Together with my assistant, I ensure the entire process runs smoothly.” After graduating in Life Sciences at the university in Geel, Belgium, he went straight to work in Arendonk. He started as an assistant, but after six months he was promoted to manager. A varied and comprehensive job he performs with pleasure every day. “Creating new life is still the best part of my profession. Seeing a healthy, viable chick emerge from an egg and then grow into a productive and sustainable laying hen.’’’
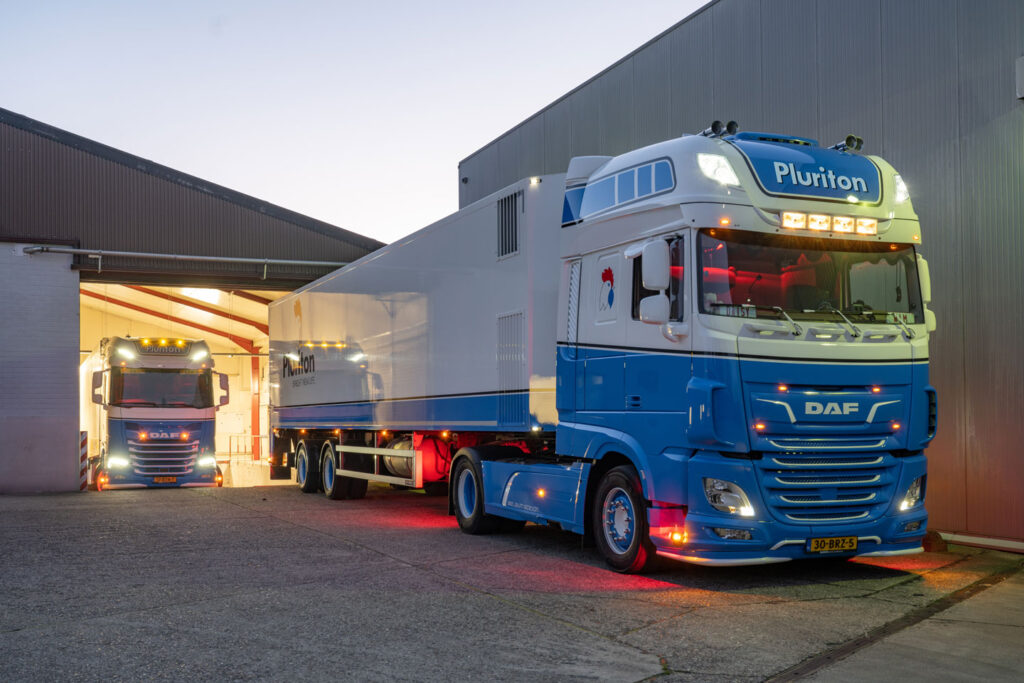
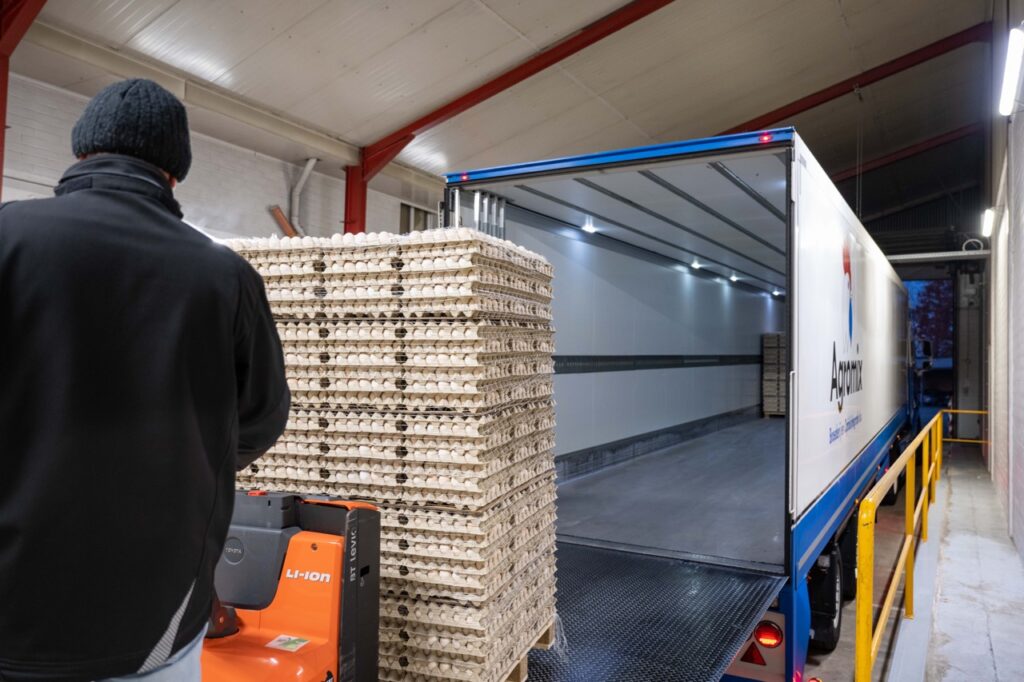

Hatching eggs and hygiene
Kevin enjoys explaining about his working day in between all his daily tasks. At around 8 o’clock a trailer from Pluriton arrives with hatching eggs from the Netherlands. The eggs are first put into storage and then disinfected. “Hygiene is absolutely paramount at our hatchery. The eggs are placed on trolleys and then disinfected with sodium hypochlorite using a special method. “We no longer use formalin for disinfection,” says Kevin. The advantage of this method is that it is less harmful to humans and animals. The disinfected hatching eggs are then placed in setters within a week of arrival. “We have a setter capacity of almost three million eggs. During the incubation process, we start at a temperature of 100° Fahrenheit and slowly reduce the temperature. The number of eggs we place in the setter depends on the customer’s specifications. We use both white or brown breeds. The majority of the hatching eggs are supplied by contracted parent stock farms and must meet strict quality standards. We always work order-based,” says Kevin. “Our customers inform us when they are ready to receive the day-old chicks and then we make sure they are delivered on time”, he says.
Hatchers
A big advantage according to Kevin is the space offered at the facility in Arendonk to candle the eggs between 15 and 19 days. That gives us greater flexibility to plan our staff. The 18 employees at the hatchery take care of the entire process from the arrival of the hatching eggs to delivering the day-old chicks to the rearing farms. There are four employees at the office who handle all the administrative tasks. Depending on the planning, we candle the eggs at 15 or at the latest 19 days. The candled eggs are placed in trays in the hatcher. “The initial temperature here is 98.5° Fahrenheit . We gradually decrease the temperature and ensure the correct humidity and CO2concentration. Climate control is essential during this process.” And Kevin believes this is the secret of being a successful hatchery manager. “It’s the part I like best of all. You always aim for the highest hatchability percentage. And you also want to see strong, viable chicks,” he concludes. Kevin is always looking to optimise this process and closely monitors the latest developments.
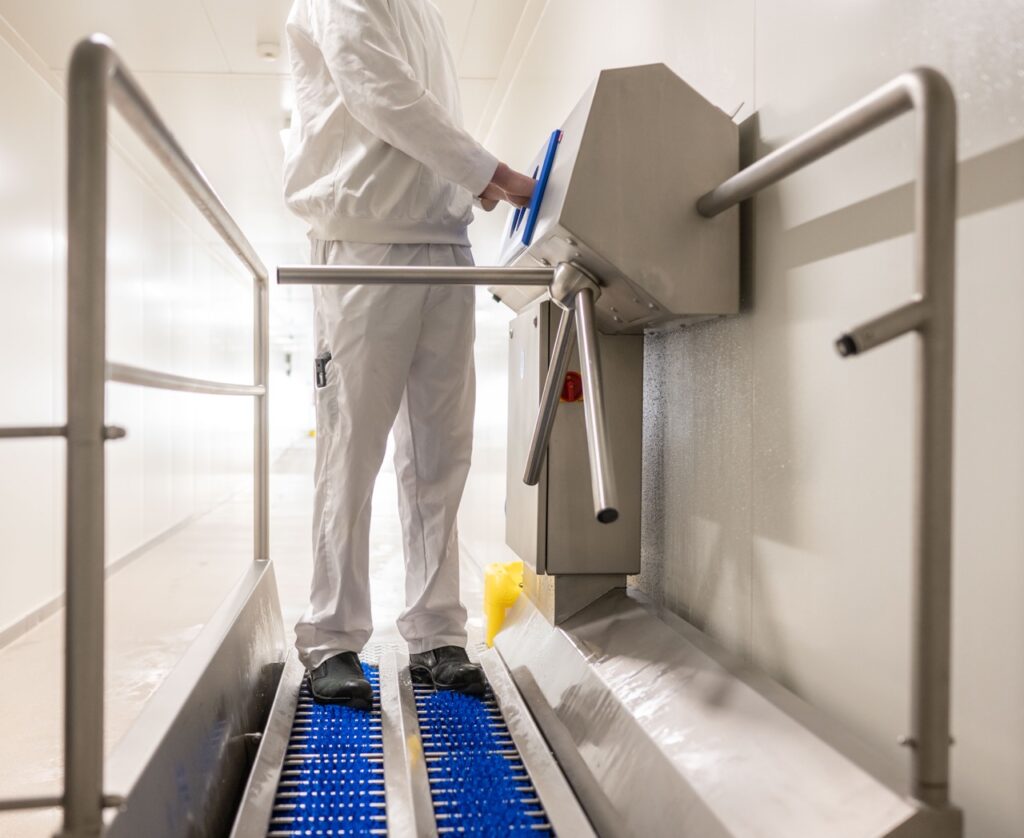
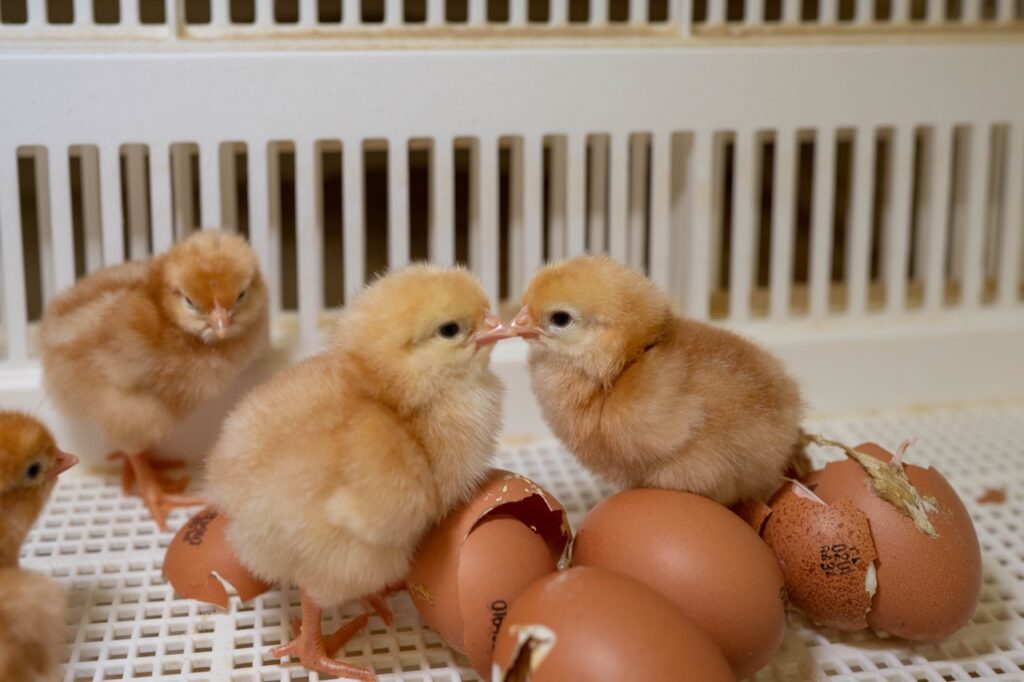
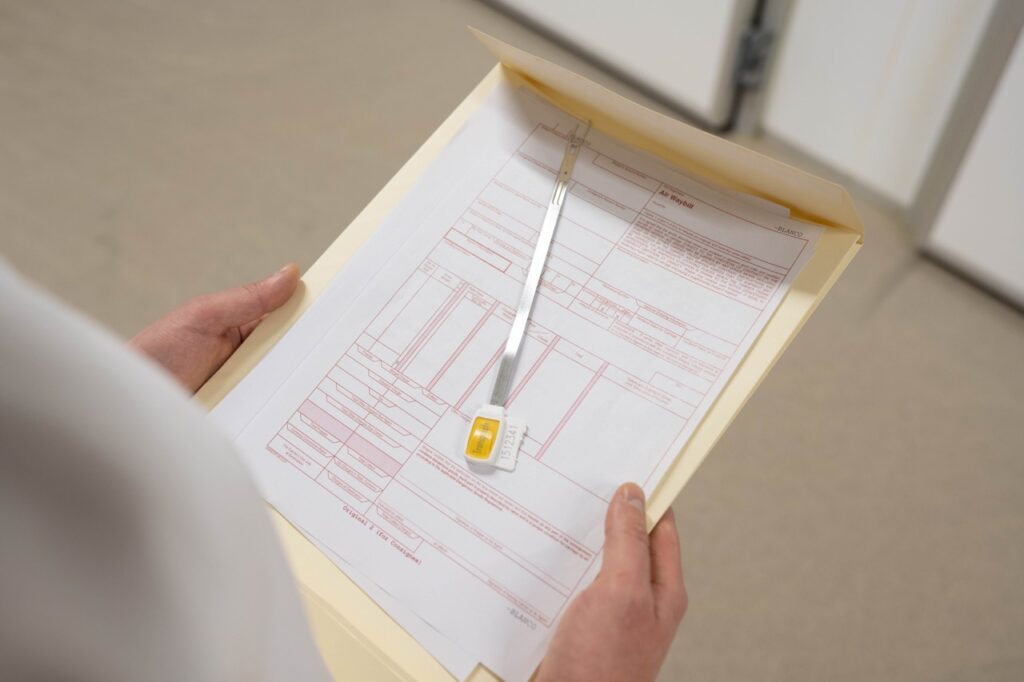
Selection and preparation for transport
After 21 days, the chicks have all hatched and the hens are selected and prepared for transport. The chicks are vaccinated and accompanied by the correct documents, depending on their destination. A special poultry transport company collects the day-old chicks and delivers them to our rearing farms. The climate conditions are monitored by sensors during transport. “In addition to healthy, viable chicks, we also provide the correct documents and monitoring, so the poultry farmer can clearly see precisely where the chicks come from and the conditions during transport. In this way, they arrive at the farmer in a healthy, good condition”.
"Creating new life is still the best part of my profession. Seeing a healthy, viable chick emerge from an egg and grow into a productive and sustainable laying hen."